精密模具制造公司应规范技工对CNC机床的正确作业。CNC技工负责按要求完成模具零部件的加工,确保安全生产,并做好机床的维护保养,延长机床的使用寿命。
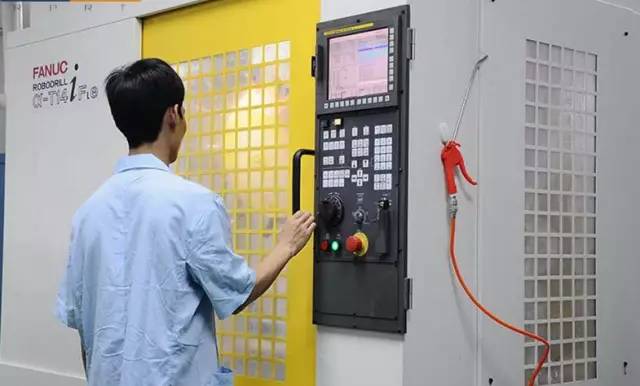
1. 机床通电开启后,注意事项如下:
- 机床通电后,检查各开关、按钮是否正常、灵活,机床有无异常现象;
- 检查电压、油压、气压是否正常,有手动润滑的部位先要进行手动润滑;
- 机床开启后,各坐标轴手动回参考点(机床原点)。若某轴在回参考点位置前已处在零点位置,必须先将该轴移动到距离原点100mm以外的位置,再进行手动回参考点或在此位置控制机床往行程负向移动,使其回参考点;
- 在进行工作台回转交换时,台面上、护罩上、导轨上不得有异物;
- NC程序输入完毕后,应认真校对、确保无误。其中包括代码、指令、地址、数值、正负号、小数点及语法的查对;
- 按工艺规程安装找正好夹具;
- 正确测量和计算工件坐标系,并对所得结果进行验证和验算;
- 将工件坐标系输入到偏置页面,并对坐标、坐标值、正负号及小数点进行认真核对;
- 刀具补偿值(长度、半径)输入偏置页面后,要对刀具补偿号、补偿值、正负号、小数点进行认真核对。
2.工件加工过程中,注意事项如下:
- 在进行高精密工件成型加工时,应用千分表对主轴上之刀具进行检测,使其静态跳动控制在3µm以内,必要时需重新装夹或更换刀夹系统;
- 无论是首次加工的零件,还是周期性重复加工的零件,加工前都必须按照图样工艺、程序和刀具调整卡,进行逐把刀、逐段程序的检查核对,尤其是对于程序中刀具长度补偿和半径补偿处,必要时再做试切;
- 单段试切时,快速倍率开关必须置于较低档;
- 每把刀首次使用时,必须先验证它的实际长度与所给补偿值是否相符;
- 在程序运行中,要重点观察数控系统上的几种显示;
- 坐标显示:可了解目前刀具运动点在机床坐标系及工件坐标系中的位置,了解这一程序段的运动量,还有多少剩余运动量等;
- 寄存器和缓冲寄存器显示:可看出正在执行程序段各状态指令和下一程序段的内容。
- 主程序和子程序显示:可了解正在执行程序段的具体内容。
- 对话显示屏:可了解机床当前主轴转速、当前切削进给速度、主轴每转切削进给、主轴当前切削载荷及各行程轴载主轴每转切削进给计算出相应刀具每刃切削量;
- 试切进刀时,在刀具运行至工件表面30~50mm处,必须在低速进给保持下,验证坐标轴剩余坐标值和X、Y轴坐标值与图样是否一致;
- 对一些有试刀要求的刀具,采用“渐进”的方法。例如,镗孔,可先试镗一小段长度,检测合格后,再镗到整个长度。使用刀具半径补偿功能的刀具数据,可由大到小,边试切边修改;
- 试切和加工中,更换刀具、辅具后,一定要重新测量刀具长度并修改好刀具补偿值和刀具补偿号;
- 程序检索时应注意光标所指位置是否合理、准确,并观察刀具与机床运动方向坐标是否正确;
- 程序修改后,对修改部分一定要仔细计算和认真核对;
- 手摇进给和手动连续进给操作时,必须检查各种开关所选择的位置是否正确,弄清正负方向,认准按键及所设定之进给速度或脉冲倍率,然后再进行操作。
3. 加工工件完毕后,注意事项如下:
- 全批工件加工完毕后,应核对刀具号、刀具补偿值,使程序、偏置页面、调整卡及工艺卡中的刀具号、刀具补偿值完全一致;在刀具重复使用时,应在对刀仪上重新对刀,可有效减小刀具磨损对加工工件影响;
- 从刀库中卸下刀具,按调整卡或程序,清理编号入库。磁盘与工艺、刀具调整卡成套入库;
- 卸下夹具,某些夹具应记录安装位置及方位,并做出记录,存档;
- 将各坐标轴停在中间位置;
- 此时若需关机,可按操作面板上之电源断开按钮,稍作等待,使主轴中主轴冷却油作部分回流后可自动关机。
免责声明:本文系网络转载或改编,未找到原创作者,版权归原作者所有。如涉及版权,请联系删